行星齒輪減速機噪音大如何降低?
行星齒輪減速機是一種運用廣泛的減速設備,產品性能好,同時具備減速范圍廣,扭矩大,精度高,噪音低等特點,但是噪音過高了不僅會影響環境,還會破壞傳動效率、傳動精度等技術指標;假如行星齒輪減速機噪音過大改如何解決呢?兆威機電公司例舉了幾種常見的影響噪音的因素和解決辦法,具體如下:
行星齒輪減速機(ji)噪音(yin)過大幾種(zhong)常(chang)見原因:
1.行星齒輪減速(su)機內部齒面硬度
隨(sui)著齒(chi)(chi)(chi)輪(lun)硬(ying)齒(chi)(chi)(chi)面技術(shu)的(de)發展,其承載能力大(da)、體積小(xiao)(xiao)、重量輕(qing)、傳(chuan)動(dong)(dong)精度高(gao)等特點(dian)使其應用領域日趨廣泛。但為獲(huo)得(de)硬(ying)齒(chi)(chi)(chi)面采用的(de)滲(shen)碳淬硬(ying)使齒(chi)(chi)(chi)輪(lun)產生變(bian)形(xing),導致齒(chi)(chi)(chi)輪(lun)傳(chuan)動(dong)(dong)噪(zao)聲增大(da),壽命縮短。為減(jian)少(shao)(shao)噪(zao)聲,需對齒(chi)(chi)(chi)面進(jin)行精加(jia)工。目前除采用傳(chuan)統(tong)的(de)磨齒(chi)(chi)(chi)方法外,又發展出一(yi)種硬(ying)齒(chi)(chi)(chi)面刮削方法,通過修正齒(chi)(chi)(chi)頂和齒(chi)(chi)(chi)根,或把主被(bei)動(dong)(dong)輪(lun)的(de)齒(chi)(chi)(chi)形(xing)都調小(xiao)(xiao),來減(jian)少(shao)(shao)齒(chi)(chi)(chi)輪(lun)嚙入(ru)與嚙出沖擊,從而(er)減(jian)少(shao)(shao)齒(chi)(chi)(chi)輪(lun)傳(chuan)動(dong)(dong)噪(zao)音。
2.行星齒輪(lun)減速機內部齒輪(lun)誤差影響
齒輪制(zhi)造過程(cheng)齒形誤(wu)差(cha)、基節偏差(cha)、齒向(xiang)(xiang)誤(wu)差(cha)和齒圈徑向(xiang)(xiang)跳(tiao)動(dong)誤(wu)差(cha)是(shi)導致行星減速(su)機(ji)傳動(dong)噪聲的(de)主要誤(wu)差(cha)。也是(shi)控制(zhi)行星減速(su)機(ji)傳動(dong)效率(lv)的(de)一個問題點(dian)。現以齒形誤(wu)差(cha)與齒向(xiang)(xiang)誤(wu)差(cha)做簡單說明。
齒形誤差(cha)小、齒面粗糙度小的齒輪(lun)(lun),在相(xiang)同試驗條(tiao)件(jian)下(xia),其(qi)噪聲(sheng)比(bi)普通齒輪(lun)(lun)要小10db。齒距(ju)誤差(cha)小的齒輪(lun)(lun),在相(xiang)同試驗條(tiao)件(jian)下(xia),其(qi)噪聲(sheng)級比(bi)普通齒輪(lun)(lun)要小6~12db。但如果有齒距(ju)誤差(cha)存在,負載對齒輪(lun)(lun)噪聲(sheng)的影響將(jiang)會減少。
齒向(xiang)誤差將導致傳動功(gong)率不是全齒寬傳遞,接觸區轉(zhuan)向(xiang)齒的(de)這端(duan)面或那個端(duan)面,因局部受力增大輪齒撓曲,導致噪聲級提高。但在高負(fu)載時,齒變形可以部分彌補(bu)齒向(xiang)誤差。
3.行星齒輪(lun)減速機系統指標檢定
在裝(zhuang)(zhuang)(zhuang)配(pei)(pei)前零部件(jian)的(de)加工精(jing)度及對(dui)(dui)零部件(jian)的(de)選(xuan)配(pei)(pei)方法(完全(quan)互換,分組(zu)選(xuan)配(pei)(pei),單件(jian)選(xuan)配(pei)(pei)等),將會(hui)影響(xiang)到系(xi)統(tong)裝(zhuang)(zhuang)(zhuang)配(pei)(pei)后的(de)精(jing)度等級,其噪聲等級也在影響(xiang)范圍(wei)之內(nei),因此(ci),裝(zhuang)(zhuang)(zhuang)配(pei)(pei)后對(dui)(dui)系(xi)統(tong)各項指標(biao)進行檢定(或(huo)標(biao)定),對(dui)(dui)控制系(xi)統(tong)噪聲是(shi)很關鍵的(de)。
4.裝配(pei)同心度(du)和(he)動平衡
裝配(pei)不(bu)同心(xin)將導致軸系運轉的不(bu)平衡,且由于齒論嚙合半(ban)邊松半(ban)邊緊,共同導致噪聲加(jia)劇。高精度齒輪(lun)傳動(dong)裝配(pei)時(shi)的不(bu)平衡將嚴(yan)重(zhong)影響傳動(dong)系統(tong)精度。
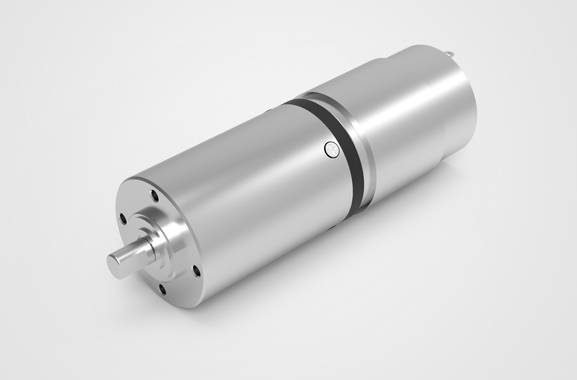
降低行星齒輪(lun)減速機噪音過(guo)大的(de)解決辦法:
1.行星齒輪(lun)減(jian)速機的(de)零件齒輪(lun)的(de)參數(shu)與(yu)結構設計對(dui)(dui)(dui)噪(zao)聲的(de)影響;一對(dui)(dui)(dui)齒輪(lun)在傳(chuan)動時(shi)。它們的(de)重(zhong)合度(du)(du)越大,那么產(chan)生的(de)噪(zao)音(yin)就越低(di)。當然重(zhong)合度(du)(du)越小其(qi)噪(zao)音(yin)也就越高(gao)。意(yi)味著(zhu)同(tong)時(shi)參與(yu)嚙合的(de)輪(lun)齒對(dui)(dui)(dui)數(shu)增多,對(dui)(dui)(dui)于(yu)提高(gao)齒輪(lun)傳(chuan)動的(de)平穩性,降(jiang)低(di)噪(zao)聲及提高(gao)承載能力都有著(zhu)重(zhong)要(yao)意(yi)義。
2.齒(chi)輪的(de)精度等級是噪(zao)聲等級的(de)重要標志(zhi);對于標準系列的(de)行星(xing)齒(chi)輪減速機來說(shuo),齒(chi)輪的(de)制造精度決定著它的(de)噪(zao)聲值(zhi)。齒(chi)輪精度越高其(qi)嚙(nie)合齒(chi)面接(jie)觸斑(ban)痕越密集(ji),整個(ge)齒(chi)面上(shang)都有(you)接(jie)觸斑(ban)痕,其(qi)噪(zao)聲越低(di)。反之齒(chi)輪精度越低(di)其(qi)嚙(nie)合齒(chi)面接(jie)觸斑(ban)痕較小,齒(chi)輪在其(qi)接(jie)觸寬度上(shang)不能完全嚙(nie)合,則運(yun)轉不平穩,甚至造成撞擊,使噪(zao)聲值(zhi)升高。
3.齒(chi)(chi)(chi)(chi)面(mian)點(dian)(dian)(dian)(dian)蝕(shi)產生的沖擊及噪聲;傳(chuan)(chuan)動齒(chi)(chi)(chi)(chi)輪(lun)受載運(yun)轉一段時(shi)間(jian)后,常常在齒(chi)(chi)(chi)(chi)面(mian)節線附近出現小塊金(jin)屬脫落,形(xing)成點(dian)(dian)(dian)(dian)蝕(shi),由于硬齒(chi)(chi)(chi)(chi)面(mian)齒(chi)(chi)(chi)(chi)輪(lun)具有承載能力大(da)、體積(ji)小、重量輕、傳(chuan)(chuan)動質(zhi)量好等優點(dian)(dian)(dian)(dian)。被廣泛應用,雖然硬面(mian)齒(chi)(chi)(chi)(chi)輪(lun)不易點(dian)(dian)(dian)(dian)蝕(shi)。但點(dian)(dian)(dian)(dian)蝕(shi)一經發生就不易跑合。齒(chi)(chi)(chi)(chi)面(mian)的點(dian)(dian)(dian)(dian)蝕(shi)會隨著工作時(shi)間(jian)增大(da)而(er)不斷地迅速擴(kuo)展(zhan)。發展(zhan)成為(wei)擴(kuo)展(zhan)性(xing)點(dian)(dian)(dian)(dian)蝕(shi)。使齒(chi)(chi)(chi)(chi)形(xing)彼此(ci)破壞(huai),增大(da)了工作噪聲和(he)沖擊。而(er)沖擊落下的金(jin)屬碎(sui)屑又加速了齒(chi)(chi)(chi)(chi)面(mian)的磨損(sun),從而(er)使齒(chi)(chi)(chi)(chi)輪(lun)傳(chuan)(chuan)遞不平穩而(er)產生噪聲。
4.齒(chi)(chi)(chi)(chi)輪加工誤差(cha)(cha)容(rong)易導致噪聲(sheng)(sheng);齒(chi)(chi)(chi)(chi)輪加工時(shi)產生(sheng)(sheng)的誤差(cha)(cha)導致噪聲(sheng)(sheng)主(zhu)要(yao)是(shi)由于齒(chi)(chi)(chi)(chi)距累積誤差(cha)(cha)及齒(chi)(chi)(chi)(chi)形(xing)誤差(cha)(cha)造成(cheng)的。齒(chi)(chi)(chi)(chi)距累積誤差(cha)(cha)是(shi)由于制(zhi)齒(chi)(chi)(chi)(chi)時(shi)齒(chi)(chi)(chi)(chi)坯的回轉(zhuan)軸(zhou)線與齒(chi)(chi)(chi)(chi)輪工作時(shi)的回轉(zhuan)軸(zhou)線不(bu)(bu)重合造成(cheng)齒(chi)(chi)(chi)(chi)輪齒(chi)(chi)(chi)(chi)厚不(bu)(bu)均勻。齒(chi)(chi)(chi)(chi)形(xing)誤差(cha)(cha)主(zhu)要(yao)是(shi)滾(gun)刀在(zai)(zai)制(zhi)造、刃磨和安裝中存(cun)在(zai)(zai)誤差(cha)(cha)造成(cheng)齒(chi)(chi)(chi)(chi)面出棱、齒(chi)(chi)(chi)(chi)形(xing)不(bu)(bu)對稱、根切及后續加工校正不(bu)(bu)充分,使齒(chi)(chi)(chi)(chi)輪傳(chuan)動不(bu)(bu)平穩。出現脈動、根切及打齒(chi)(chi)(chi)(chi)現象進而產生(sheng)(sheng)噪聲(sheng)(sheng)。
5.內齒(chi)(chi)圈(quan)及行(xing)星(xing)架(jia)加(jia)工誤差(cha)導致噪聲;內齒(chi)(chi)圈(quan)徑(jing)向(xiang)跳(tiao)動(dong)誤差(cha)對(dui)浮動(dong)件的(de)浮動(dong)量影響(xiang)大。因此(ci)對(dui)其(qi)內齒(chi)(chi)圈(quan)徑(jing)向(xiang)跳(tiao)動(dong)量應嚴格(ge)控(kong)制。內齒(chi)(chi)圈(quan)由(you)于加(jia)工和(he)熱(re)處(chu)理(li)工藝(yi)選擇不當。造成(cheng)熱(re)處(chu)理(li)后齒(chi)(chi)形、齒(chi)(chi)向(xiang)及齒(chi)(chi)距等參(can)數都(dou)發生變(bian)化也(ye)是導致噪聲重要原因之一。行(xing)星(xing)輪架(jia)加(jia)工過程(cheng)中行(xing)星(xing)輪軸位(wei)置度(du)偏差(cha)直接影響(xiang)齒(chi)(chi)輪副的(de)側隙.必要的(de)側隙對(dui)減速(su)機的(de)正常運轉、潤滑、熱(re)脹冷(leng)縮不卡(ka)堵十分重要,但側隙過大會(hui)在正反轉換向(xiang)時(shi)產(chan)生沖擊從而產(chan)生噪聲。
6.重(zhong)(zhong)載(zai)齒(chi)輪傳動齒(chi)面(mian)(mian)彈(dan)性(xing)變型導致噪(zao)(zao)聲(sheng);重(zhong)(zhong)載(zai)齒(chi)輪特別(bie)是硬齒(chi)面(mian)(mian)齒(chi)輪,其彈(dan)性(xing)變形很大,跑合性(xing)能又極差,齒(chi)輪受載(zai)變形引起的嚙入(ru)嚙出沖擊(ji)產生噪(zao)(zao)聲(sheng)。
7.裝(zhuang)配(pei)(pei)誤差導(dao)致噪聲 ;裝(zhuang)配(pei)(pei)時幾何(he)精度(du)未達到(dao)設計要求(qiu)。導(dao)致傳(chuan)動(dong)(dong)系統(tong)發生(sheng)振動(dong)(dong)產生(sheng)噪聲,或者裝(zhuang)配(pei)(pei)時由于個別零部件的松(song)動(dong)(dong)。導(dao)致系統(tong)定位(wei)不(bu)準。處于非正常位(wei)置嚙合。軸(zhou)系移動(dong)(dong)產生(sheng)振動(dong)(dong)和噪聲。
8.整機維護不當導致噪(zao)聲 ;齒輪(lun)嚙合時產(chan)生齒面(mian)磨(mo)損(sun)。行星齒輪(lun)減(jian)速(su)機在(zai)長(chang)期使用(yong)過程(cheng)中,如果潤滑、冷卻不充分,潤滑油清潔度差(cha),會加速(su)磨(mo)損(sun)。當磨(mo)損(sun)嚴(yan)重時,齒輪(lun)精度受到破壞。行星齒輪(lun)減(jian)速(su)機噪(zao)聲會增加。